SHOTCRETEINTRODUCTION
It is generally accepted that the term “shotcrete” has been adopted in Australia for the description of sprayed concrete in accordance with the American Concrete Institute (ACI) conventions, and the term “shotcrete” will be used throughout these pages. In this document, the term “shotcrete” is defined as mortar or concrete conveyed through a hose and pneumatically projected at high velocity onto a surface or substrate. It is synonymous with the term “sprayed concrete” used in Europe and some other locations.
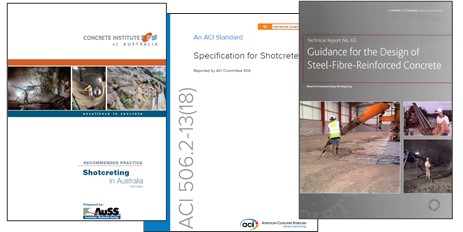
Wet & Dry
There are two types of shotcrete processes, as described below.
Wet-mix Shotcrete Process
This is a technique in which cement, aggregate, and water are batched and mixed together prior to being delivered into a pump and conveyed through a hose to a nozzle where it is pneumatically projected onto a surface. Compressed air is introduced to the material flow at the nozzle in order to project the material toward the substrate. Wet shotcrete normally incorporates admixtures and may also include fibres.
Dry-mix Shotcrete Process
This is a technique in which cement and aggregates are batched, mixed and delivered into a purpose-made machine wherein the materials are pneumatically conveyed through hoses or pipes to a nozzle where water is introduced to wet the mixture before it is projected pneumatically into place. The shotcrete may also include admixtures or fibres or a combination of both. Table 1.1 describes the characteristics of the two processes. It is generally accepted that within Australia the majority of shotcrete is applied by the wet–mix method, however certain applications are more suitable for dry-mix
SHOTCRETETECHNOLOGY
The following terms are commonly used to describe aspects of shotcrete technology in Australia:
Accelerator – a material that is normally added at the shotcrete nozzle having the primary effect of causing rapid stiffening, reducing slump and increasing the rate of hydration of the cement. The term activator is also used to denote a set accelerator. Accelerators normally used for shotcrete are chemically distinct from admixture accelerators used in cast concrete applications.
Additive – pigments or oxides added to a cementitious mixture.
Adhesion/Bond – the property that quantifies the chemical and mechanical strength of the shotcrete sticking to the substrate.
Binder – all cementitious materials in a concrete mixture.
Bleeding – the movement of the water from within to the surface of the shotcrete resulting from the separation of water from the solid ingredients in the mix.
Blended cement – A hydraulic cement consisting of Portland cement and more than 7.5% of fly ash or GGBS or both, and up to and including 10% amorphous silica all uniformly mixed. The proportions are at the discretion of the cement manufacturer.
Build-up – the increase in thickness with successive passes of shotcrete.
Cement – (see Hydraulic cement, General purpose cement and Blended cement).
Chemical Admixture – a liquid or dispersible powder added deliberately to concrete before or during mixing to improve its economy and / or properties in the plastic and / or hardened state.
Cohesion – the extent to which the ingredients of mixed concrete, mortar or shotcrete remain homogeneously mixed when transported, handled, placed, pumped and / or sprayed. This term also refers to the extent to which particles in a mixture stick to each other.
Compaction – the process of reducing and ideally eliminating the entrapped air during placing of shotcrete through sufficient air pressure and proper spraying techniques.
Concrete – A mixture of cement, aggregates and water, with or without the addition of chemical admixtures, or other materials, in which the nominal maximum aggregate size is equal to or greater than 5 mm.
Curing – the process of maintaining freshly placed concrete or sprayed shotcrete in a moist condition and, where possible, at ideal temperature conditions to enhance and ideally facilitate complete hydration of hydraulic cement and the reactions of any pozzolanic materials to allow the potential properties of the mix to develop.
Delamination – loss of bond between a layer of shotcrete and either the substrate or previously applied shotcrete.
Dental Shotcrete – A layer of shotcrete applied to an over-excavated or broken substrate building it back up to the required design line.
Dry-mix Shotcrete – Shotcrete in which all the ingredients are conveyed in a dry state by compressed air to the nozzle, where water is added, and the resultant shotcrete is sprayed via compressed air.
Embrittlement – a phenomenon is afflicting FRS in which fibre bond strength increases to such a high level with ageing of the concrete matrix that the mode of post-crack behaviour changes from a high energy pull-out mode to a low-energy rupture mode. This leads to a loss of performance at relatively wide crack widths and therefore primarily affects strength limit state considerations.
Fall out – a substantial piece or slab of shotcrete that falls away from a sprayed surface some time after spraying. This is not to be confused with rebound that involves particles which bounce off the substrate or in-place shotcrete during the shotcreting process.
Fibres – slender reinforcing elements typically of high tensile capacity added to concrete. See Macro fibres and Micro fibres.
Flash coat – a thin shotcrete layer applied for sealing or bonding purposes.
FRS – Fibre Reinforced Shotcrete
General purpose cement – is a hydraulic cement containing a minimum of 92.5% Portland cement and a maximum 7.5% combination of mineral additions and / or minor additional constituents (5% maximum).
Gunite – the brand name given by the Cement Gun Company in 1907 in the USA to the first mortar that was sprayed. This mortar contained fine aggregate and a high percentage of cement. The term Gunite is not generally used in Australia.
Hydration – the chemical reaction of hydraulic cement with water during which compounds exhibiting mechanical strength are formed.
Hydraulic cement – a binding material that sets and hardens by chemical reaction with water and is capable of doing so underwater. The most common form of hydraulic cement is general purpose (GP) cement.
Mortar – as for Concrete except “the maximum nominal aggregate size is less than 5 mm”.
Macro fibres – relatively large fibres normally used to develop structural levels of performance after cracking of the concrete matrix.
Micro fibres – relatively small diameter fibres, usually less than 0.3 mm diameter, used for control of plastic shrinkage cracking and rebound.
Micro-synthetic monofilament polypropylene fibres – very small diameter fibres made of polypropylene used to control explosive spalling in high temperature exposure.
Nozzle/gun finish – the undisturbed finish of shotcrete as applied from the nozzle.
Nozzleman – the person charged with control of the nozzle and therefore the spraying of the concrete. The term “sprayer” is used in place of “nozzleman” in this document.
Overspray – shotcrete inadvertently deposited on areas surrounding the intended surface.
Over-thickness – extra shotcrete build-up deposited in excess of the intended thickness.
Pass – movement of the nozzle over an area of application during shotcreting (a layer of shotcrete is built up by making several passes).
Paste – a combination of the finely divided solid material that passes the 300 micron sieve (0.03 mm), plus available fluids, in the concrete mix.
Post-crack performance – either the energy absorption or residual strength of a fibre reinforced concrete material or element.
Pozzolan – a material consisting mainly of silicates that together with lime and water forms compounds possessing cementitious properties.
Performance based specification – a specification in which the performance characteristics required of the shotcrete are specified (e.g. compressive strength at a particular age of the shotcrete, flexural strength, toughness, relative density, etc).
Permanent lining – shotcrete that is required to satisfy serviceability and strength performance requirements over the design life of the entire structure. This design life is typically 50–120 years depending on the type of structure.
Prescriptive specification – a specification where the nature and/or the quantity of some or all of the shotcrete ingredients and the process by which the shotcrete is produced and applied are specified (e.g. cement content, etc).
Primary Lining – a shotcrete lining installed as part of the initial tunnel excavation and support cycle in accordance with the relevant requirements shown on the relevant Design Drawings.
Pulsing – pulsating or intermittent flow of shotcrete material through the delivery line.
Rebound – that part of the shotcrete which ricochets away from the intended surface during the spraying process. Rebound consists mainly of larger aggregate particles, and to a lesser extent, fibres, binder and water.
Residual strength – the flexural or tensile strength of a fibre reinforced concrete after cracking of the matrix.
Sand lens/pocket – a zone within the shotcrete containing unmixed fine aggregate with little or no cement, resulting from inadequate mixing of the delivered concrete.
Sagging or sloughing – downward movement of the shotcrete from its initial and required point of application.
Segregation – separation of aggregate particles from the paste prior to spraying.
Saturated Surface Dry (SSD) – condition of an aggregate when the permeable pores are filled with water and no water is on the exposed surface.
Sacrificial Layer – a layer which is not considered to contribute to the structural resistance of a lining in the permanent case due to an effective section loss in the surface zone caused by the corrosion of steel fibres or loss of concrete during a fire.
Secondary lining – a tunnel lining installed independent of the excavation and support cycle, e.g. to supplement the lining thickness in areas where embedded steel elements cannot be considered to contribute to the permanent support, and/or, shotcrete lining installed after a waterproofing membrane has been placed.
Serviceability Limit State (SLS) – A limit state is a condition of a structure beyond which it no longer fulfils the relevant design criteria. The serviceability limit state is exceeded for a structure if it fails to meet performance requirements for use under service loads even though it may satisfy strength related performance requirements and thereby avoid collapse. A shotcrete structure is generally deemed to satisfy the serviceability limit state when the constituent elements satisfy limits on maximum allowable stress, deformation, and crack width in response to service loads.
Smoothing layer – a thin layer of shotcrete (or mortar) usually intended to provide a more uniform and smoother surface generally applied over a layer of shotcrete.
Sprayer – the person charged with control of the nozzle and therefore the spraying of the shotcrete.
Substrate – The surface on to which the shotcrete is sprayed.
Supplementary cementitious materials (SCM) – primarily silicate-based materials that contribute to the binding properties of hardened concrete through hydraulic or pozzolanic activity. Typical examples are fly ashes, GGBS (ground, granulated blast-furnace slag), and silica fume.
Temporary lining – a shotcrete lining that is required to satisfy strength performance requirements over the anticipated construction time for a structure. This anticipated construction time is typically 1–5 years. Serviceability limits are normally not applied to temporary shotcrete.
Toughness – Post-crack performance of fibre reinforced shotcrete defined as post-crack energy absorption of a test specimen.
Ultimate Limit State (ULS) – the ultimate limit state for a structure is exceeded if it fails to satisfy strength-related performance requirements in response to design loads and is therefore at risk of collapse. A structure is deemed to satisfy ultimate limit state criteria if all factored bending, shear and tensile or compressive stresses are less than the factored resistance calculated for all sections under consideration.
Water/cement ratio – the ratio of the mass of water, exclusive of that absorbed by the aggregate, to the mass of cement in a mixture, stated as a decimal, and abbreviated as w/c.
Water/binder ratio – the ratio of the mass of water, exclusive of that absorbed by the aggregates, to the mass of all binding materials comprising cement and supplementary cementitious materials.
Water-proofing membrane – a spray-applied or sheet membrane included with a shotcrete lining to reduce the penetration of water.
Wet-mix shotcrete – shotcrete in which all of the ingredients, including the mixing water, are mixed before being pumped into the delivery line and sprayed.
SHOTCRETEUSES
Shotcrete plays an essential role in today’s building industry, civil construction and mining industries. It is an exceptionally versatile material that can be easily and rapidly applied to provide a cost-effective means of construction. Shotcrete is an efficient way of placing concrete and forms an excellent bond to a number of substrates including rock, concrete, masonry and steel. It is suited to a wide range of ground-support applications, linings, and building structures.
The main advantages of shotcrete over conventionally placed concrete are:
Placement and compaction are carried out as one operation.
Formwork is generally eliminated.
The process of placement can be quicker in most projects.
Following application and an initial period of hydration, shotcrete provides early passive support to the ground. As the shotcrete hardens and gains strength, subsequent deformation generates a significant resistance because the shotcrete also becomes rigid.
Properly designed and applied shotcrete remains in place without sagging even in vertical wall and overhead applications. It is especially suited to areas with restricted access by the use of small portable or mobile equipment. Shotcrete is either applied using remotely controlled or hand-operated equipment. Remotely controlled equipment is generally used in underground applications to allow safe operation by the nozzleman away from the unsupported area. These advantages have resulted in shotcrete being used for a variety of applications, some of which are listed below, grouped in general areas of application.
Tunnelling
In tunnelling, shotcrete can be used either for the final lining or as temporary support as the tunnel is advanced. Final linings of fibre-reinforced shotcrete can be in the form of a Single Pass Tunnel Lining (SPTL) using a combination of rock bolts, cable bolts, fibre reinforced shotcrete, and steel arches (where additional support is required). Shotcrete thicknesses can vary from 50 mm to 500 mm, and can be applied in several layers. Shotcrete applied as temporary support should be designed to provide early structural support. This can be followed later by a second layer to provide permanent support. The permanent support lining may take the form of shotcrete, precast concrete segments, or cast in place concrete.
As shotcrete technology has developed and waterproofing systems improved, SPTL has become a significant method of ground support for civil tunnel construction. Thin unreinforced shotcrete linings can also be applied to smooth the rock surface and hence reduce resistance to air-flow.
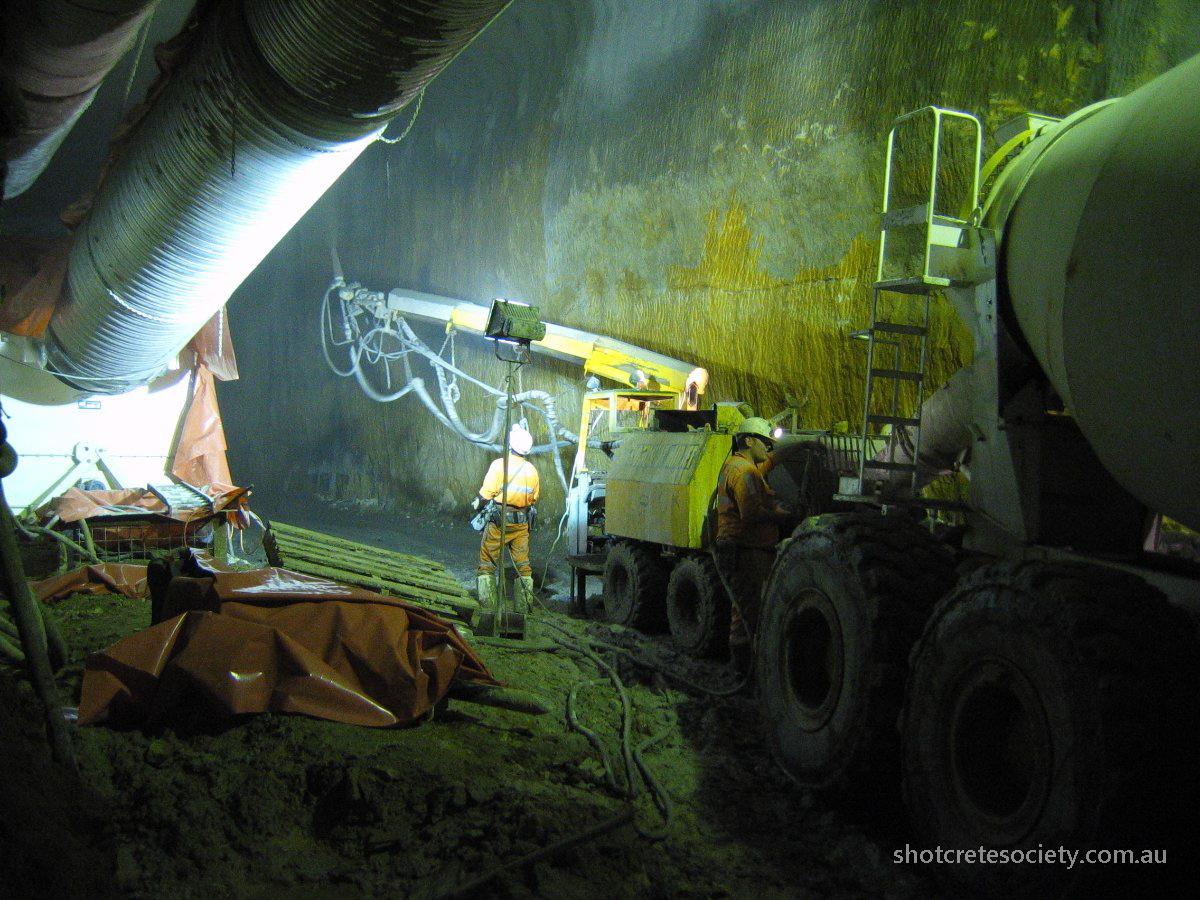
Caverns
Underground caverns for storage of commodities and materials such as oil, gas, effluent and nuclear waste have been built with the use of permanent shotcrete linings, e.g. the Elgas gas caverns and North Side Storage Tunnel – both in Sydney.
Ground Support in Mining
Mechanised application of shotcrete in Australian mines first occurred in 1972. Initially, shotcrete was applied over installed mesh and bolts in areas of bad ground where mesh alone was inadequate. However, FRS progressively replaced mesh as the preferred method of ground support in underground mines during the 1990s due to the following reasons:
The effectiveness of ground support achieved with FRS and post-bolting significantly exceeded the effectiveness of ground support achieved with bolts and mesh.
Increased safety achieved by not exposing personnel to unsupported ground.
The speed of mining development improved using shotcrete.
The proportion of rehabilitation of ground support was reduced significantly.
The increased availability of mechanised spraying equipment and reduced labour requirements in the ground support process.
One of the key developments that improved the efficiency of using shotcrete for ground support was the move to in-cycle shotcreting. In this process the shotcrete was applied during the development cycle, after blasting and before the installation of rock bolts. In this way, the use of mesh was not required and the bolts were installed through the shotcrete layer. This method resulted in the bolt plates being installed over the shotcrete layer, providing a superior load transfer connection between the shotcrete layer and the ground.
Installing the shotcrete during the development cycle demanded that the shotcrete achieve substantial early age strength as soon as possible after application to allow the safe re-entry of personnel to continue development. The required early strength must be determined by the mining engineer on each site but is generally in the order of 1.0 MPa. This can normally be achieved in 3-4 hours after spraying. The effectiveness of the shotcrete layer for ground support can be improved by increasing the thickness of the applied layer and/or by increasing the fibre dose. Hence one application system can cope with many different design requirements.
In areas that are seismically active it is common practice to place a layer of un-encased mesh fixed with rock bolts over the final shotcrete layer. When a seismic event occurs there is a release of energy producing seismic waves that radiate outwards, these waves travel through the rock and when the magnitude of the peak particle velocity exceeds the resistance of the shotcrete they can force the shotcrete as well as the fractured rock behind the shotcrete into the excavation. The ductility of un-encased mesh can greatly reduce the damage. It should be noted that by encasing the mesh it not only reduces the ductility of the mesh but the encasing becomes a potential projectile further endangering any person or equipment in the tunnel at the time. Today the vast majority of underground mines in Australia use shotcrete for ground support.
Commercial Buildings
Shotcrete has a history of application in the construction of buildings. Typical shotcrete applications include underground load bearing elements and above ground load bearing elements within multi-storey structures. Other examples are perimeter lateral stability elements and internal load bearing walls to reduce the amount of traditional columns in a structure. Shotcrete has been used as an alternative to cast tilt-up panel construction for portal-framed structures and aggregate silos.
Ground Excavation for Basements and Car Parks
Shotcrete plays an important role in ground support for excavations, where “boundary to boundary” or vertical cuts are required. Coupled with soil nails or piles & anchors, top down construction is achieved as excavation proceeds delivering the in-place permanent basement walls upon conclusion of the excavation to the finished floor level.
Backfill of Subsidence or over Excavated Surfaces
Shotcrete can be effectively used to backfill areas of over-excavation or subsidence. Traditional methods such as one-sided formwork could require personnel to be exposed to dangerous conditions as well as presenting logistical difficulties for access and construction.
One example is the Shannon Creek Dam spillway walls (completed September 2008). The dam walls were steeply inclined and up to 11 m high. The specification for the formed and poured walls was replaced by an alternative shotcrete design. Overbreak was prevalent due to unavoidable ground conditions & challenging excavation angles. Coupled with a double layer of reinforcement this made quality compacted shotcrete application difficult. To solve this, a shotcrete blinding layer was applied to bring the substrate back to line. The reinforcement was then installed and the shotcrete applied and finished with excellent compaction, increased productivity and reduced cost.
Complex Civil Structures
Shotcrete is highly suited to structures involving complex geometry, including curved or folded sections. Typical applications include the construction of lightweight roofs, theme parks, zoos.
Channels/Reservoirs and Spillways
Reservoirs and channels can be constructed by excavating the shape required and spraying concrete free-form directly onto the exposed rock or earth. Shotcrete has the ability to be placed, compacted & finished (possibly in one pass) in instances requiring high access, free form or very thick linings. Examples are the Olympic Whitewater Stadium Channel in Sydney and Shannon Creek Dam Spillway in Grafton NSW.
Embankment Stabilisation
Shotcrete is widely used for the stabilisation and protection of surface rock and earth. The surface is protected against deterioration by filling in uneven parts and sealing the entire surface. Due to its high shear strength and good bond to rock, shotcrete stabilises loose rock by filling gaps and cracks and thereby prevents loose pieces of rock from falling out. This can prevent progressive surface failure. Shotcrete is most effective when used in conjunction with rock or soil anchors.
Swimming Pools and Skateboard Parks
These recreational structures are good examples of free-form construction using shotcrete. Both pools and skateboard parks are constructed by excavating a hole in the ground to the required shape, fixing a top board to form the rim, positioning the necessary reinforcement, and shotcreting the structure. Constructions of this type are economical, strong, rigid and durable.
Refractories
Furnaces of all types can be lined or repaired with special blends of shotcrete containing materials such as high-alumina cements and crushed firebricks, which possess enhanced refractory properties. One of the main advantages of refractory shotcrete is that it can be placed quickly and in large volumes in almost inaccessible areas, for example, at height inside chimneys or in remote parts of large furnaces.
Repair, Restoration, and Strengthening
Shotcrete can be readily used for the reinstatement of damaged structures. Repair of deteriorated concrete caused by corrosion or spalling, and concrete damaged by fire, are typical applications. Repair and restoration can only take place after the affected areas have been properly identified and prepared. Structures suitable for repair using shotcrete may include bridges, culverts, sewers, dams, towers, ports, buildings, and steel structures. Existing concrete structures can be strengthened with shotcrete where construction of the original concrete, for example, may need to be partially cut out and replaced due to honeycombing.
Shotcrete can also be used when a structural element needs to be increased in size for the purpose of increasing load capacity. Structural elements that can be strengthened by this means include beams, columns, slabs, masonry walls, tanks, and pipes.
Fire Proofing
The use of shotcrete as a fireproofing material is common, especially in chemical plants and oil refineries. This process can involve the encasement of steelwork or an increase in thickness of cover concrete using shotcrete. Moreover, shotcrete can be designed to incorporate polypropylene micro fibres to minimise spalling under extreme heat conditions. High temperatures melt the micro fibres allowing water vapour to travel through the voids that were thereby formed and dissipate to the surface, hence minimising internal pressure build up and subsequent spalling.
Decorative Finishes
Shotcrete is most economically applied as a free-form material with an as-placed finish. Smooth surfaces, sharp edges and the like can be provided but they can be costly to produce and rely strongly on on-site workmanship. Natural-look finishes, such as the blocky sandstone of Sydney can also be achieved. When finishing coats are applied, they can be sprayed and carved over various existing structures. They can also be coloured to match the surrounding areas.
Bridge Abutments and Drainage Walls
Concrete Bridge abutments or Deflection walls can be extremely challenging to construct with conventional formwork for cast in-situ concrete. Height, access and securing and positioning formwork (which is generally one-sided) required to place the concrete can, depending on the project, be almost impossible and generally impractical.
Shotcrete offers substantial cost and time savings and can be applied at almost any height, angle or thickness and negates the use of the installation and removal of formwork shutters in this regard. The following pictures demonstrate shotcrete’s versatility and advantages for both of these applications.
Matching or Replacing Concrete Elements
The architectural versatility of shotcrete means that it can readily be made to match the appearance of cast concrete. An example of this is the replication of pre-cast concrete panels by employing the shotcrete that is required for excavated ground support, negating the need for secondary panels. The North West Rail Link infrastructure project in north-west Sydney required large areas of walls to be stabilised during excavation employing soil nails coupled with structural shotcrete walls. The shotcrete was installed in top-down construction and, by cutting, finishing and installing specific jointing, the contractor was able to emulate the appearance and thus preclude and match exact pre-cast panels required for the Reinforced Earth bridge abutments (Figure 1.22). Time and cost savings were substantial as no secondary work involving transport, cranes, labour, and the panels themselves were required.
Smoothing Layers
Wet or dry shotcrete can be applied as a non-structural smoothing layer for many reasons:
To fill voids where required.
To improve airflow in air plenums.
To reduce quantities of sprayed membrane required for waterproofing.
To overcome puncturing or damage to either sprayed or sheet membranes due to the presence of protruding fibres in the structural shotcrete mix.
As an example, initial shotcrete layers required for tunnel roof support are often rough and dimpled due to their aggregate size coupled with a gun finish. Where waterproof membranes are specified to be sprayed over the initial lining they require only a thin layer typically 4–6 mm. Without a smoothing layer containing fine aggregates membrane wastage is excessive and costly.
SHOTCRETEHISTORY
The first milestone in the history of shotcrete occurred in 1907 when a machine was invented by Carl Ethan Akeley in the USA (Yoggy, 2000). This machine allowed dry materials to be placed pneumatically with the addition of water at the nozzle. In 1910, a double chambered cement gun, based on the design by Akeley, was introduced into the construction industry. “Gunite”, consisting essentially of sprayed mortar, was used in the USA in the 1920s to fireproof mine drifts.
The early 1930s saw the generic term “shotcrete” introduced by the American Railway Engineering Association to describe the Gunite process. In 1966, the American Concrete Institute (ACI) adopted the term shotcrete for all pneumatically applied mortar and concrete involving both the dry-mix and the wet-mix processes. In England and Australia the term Pneumatically Applied Mortar (PAM) was often used in place of the term ‘shotcrete’. The European Union terminology for the same material is “sprayed concrete”. In the 1940s coarse aggregate (10 mm minus) was introduced into sprayed concrete mixes. The wet shotcrete process was introduced in 1955. In the late 1960s remote-controlled shotcrete equipment was introduced. Steel fibres were first introduced in 1971 in North America, and in 1977 the Norwegians introduced steel fibres in combination with remotely controlled application on a large scale.
Shotcrete was first used in Australia in 1914 for construction of tank walls in a water reservoir in Sydney. Spraying equipment started to be manufactured under licence in Australia in the 1920s, and its use spread to applications including dry dock and channel construction. In the 1950s several hydro-electric and water catchment projects in Victoria were constructed using shotcrete, including the Kiewa and Tarago tunnel projects, and agricultural channels in Werribee and Wimmera. Ground stabilisation with PAM was undertaken for the Ettalong dam project in Victoria in the late 1950s, plus the Snowy Mountains Hydro-Electric Scheme including the Island Bend and Geehi pressure tunnels constructed in the early 1960s. Shotcrete has been widely used for hydro-electric projects in Australia ever since.
Swimming pools were first constructed using shotcrete in the 1960s. In 1980, Sandy Hollow Rail Tunnel in NSW was lined using steel-fibre reinforced wet shotcrete. In the 1970s a small amount of dry-spray shotcrete was used in underground mines including the Dolphin Scheelite Mine at King Island, and the Tower Colliery and Darkes Forest coal mine in the Illawarra. In the 1980s it was used at the Rosebery Mine in Tasmania, and then the Broken Hill, Woodlawn and Perseverance Mines in the 1990s. Since the late 1990s the increase in the use of wet-mix fibre-reinforced shotcrete in underground mines has been extremely rapid.
In 2018 around 500,000 m3 was used annually for underground construction in tunnels and mines, and around 300,000 m3 in civil basements, pools, embankments, etc. In 2014, shotcrete use increased substantially in underground coal mines and now forms a major part of ground, methane, and dust control in this environment.
Major infrastructure projects in Australia that have used shotcrete in their construction include North West Rail Link, WestConnex, New M5, Northconnex, North Strathfield Rail Underpass, St Helena Tunnel (T2E), Sydney Metro Rail Tunnel, Melbourne Metro Rail Project, WestGate Road Tunnel Project, Forrestfield Airport Link Project Perth, T2T, Adelaide Hospital, Darlington Upgrade, Super Highway, Torrens Rail, South East freeway, Northern Corridor, Goodwood intersection Sydney Airport Rail Link, Sydney Eastern Distributor, Melbourne City Link, Vulture St Brisbane, Crafers Tunnel South Australia, Sydney M5 East Motorway, M2 Motorway Sydney, Epping to Chatswood Rail Line, Lane Cove Tunnel, Cross City Tunnel in Sydney, Clem Jones Tunnel, Airport Link Tunnel, Boggo Road Busway Brisbane, Tugun Bypass Queensland, Brunswick to Yelghun Highway NSW, Mount Conjola road Deviation, East Link Project Melbourne, Cronulla Rail line Duplication and Shannon Creek Dam Grafton NSW.
Shotcrete is now widely used to construct swimming pools, facilitate slope stabilisation-retaining structures and for various architectural work. Repair and remediation is a relatively small-scale application for shotcrete in Australia.